7 min read
ASSET TRACKING BENEFITS: More Than A Way to Find Missing Equipment
By: Elizabeth Sholes on Jun 7, 2021 11:15:00 AM
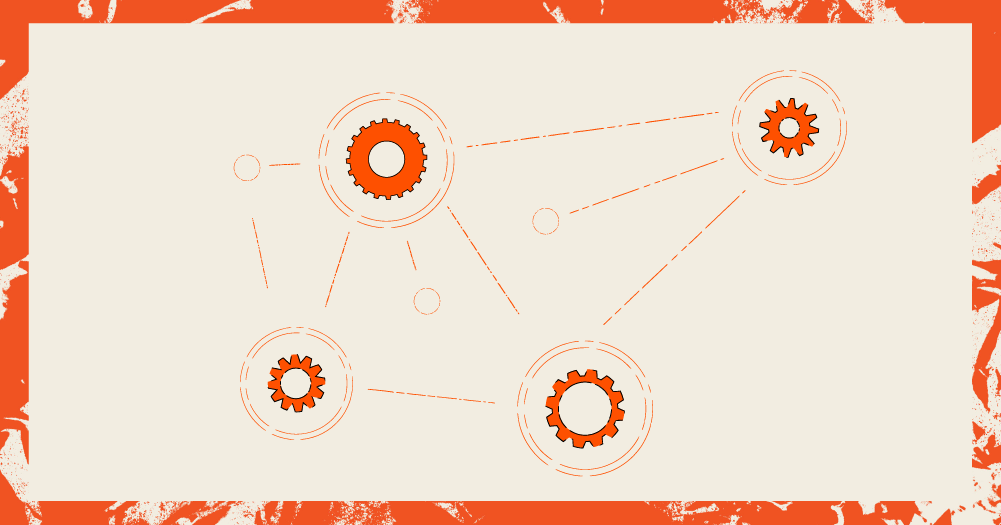
Asset tracking is hot. In many industries it’s quickly becoming a must-have. Manufacturers, shippers, retailers and even hospitals are embracing this versatile piece of technology to keep tabs on vehicles, equipment and people. It’s estimated that by 2027--just six short years away--across the globe there will be 267 million asset trackers in use.
For fleet owners and contractors who are debating whether or not to add asset tracking technology to your operational toolbelt, consider this: Asset tracking is much more than a way to find lost or stolen equipment or identify rogue dump truck drivers.
It’s a way to learn more about your particular business through data.
Whether the GPS tracking is done through the use of telematics or smart devices, it all boils down to the systematic collection of useful information. Your specific information. That way it’s reliable and accurate and takes the guesswork out of decision making.
For example, you may have a hunch that your drivers are punching in early or taking breaks too often, but without knowing for sure, what can you do about it? Unfortunately, not much. But with real-time asset tracking in place, you can see exactly what’s going on. You can trust the data. And take action.
One of the major asset tracking benefits is that it will give you insights to help you manage and prioritize these common challenges:
- How will I increase asset utilization and customer satisfaction?
- How can I save money on the road and in the back office?
- How do I improve efficiency in the areas of scheduling and dispatching?
- And how should I optimize my operations?
Asset tracking technology is an indispensable multi-function tool--you can think of it as the Swiss army knife of logistics solutions. With asset tracking, you’ll be well prepared for the unexpected and rocky wilderness of the construction landscape.
Improve Visibility with Asset Tracking
Of course one of the most obvious benefits to having asset tracking in your back pocket, so to speak, is the ability to know the location of your assets in real-time. With GPS tracking technology, you’ll be able to see with razor sharp precision if those assets are where you expect them to be--progressing along the correct route, arriving at the scheduled jobsite or parked safely in the yard.
Knowing the whereabouts of your vehicles and equipment at any and every moment in time helps you better utilize your assets. When a dump truck finishes a job ahead of schedule, you have all the information you need to quickly get it reassigned. Every hour your trucks are not working at an acceptable rate is an hour your asset depreciates without generating revenue. No one wants that.
Asset tracking data can help you improve your asset utilization ratios.
In addition to optimized asset utilization, another advantage of increased visibility involves your customers. Being able to pinpoint a vehicle’s location is key to improving customer service. When you can consistently provide your customers with accurate ETAs and timely updates, you’ll see more repeat business and referrals rise.
Data collected through asset tracking helps you grow your client base.
Save on Costs with Asset Tracking
If keeping track of assets is like the basic blade of those handy pocket knives, then saving costs is like the reamer tool cleverly fitted beside it. Admittedly, most fleet operators and construction professionals add asset tracking to their business operations for its main purpose--locating vehicles and equipment. But they quickly gain an appreciation for a surprising benefit from the technology--increased savings.
Generally, after a relatively short period, users welcome this finance-related advantage of tracking solutions. The value stems from the exactness provided by digital technology. Before making the switch to an asset tracking platform, fleet operators and others were stuck with the old method of time tracking where drivers rounded up to the nearest quarter-hour.
But now, many asset tracking solutions, like the TRUX all-in-one dispatch management platform, include a digital punch-in and punch-out feature. The time drivers spend traveling to and from worksites is tracked down to the minute. So instead of paying for those mystery time slots on each end of a shift, you can be sure you’re paying for the actual time worked. No more worries about overpaying.
This digital punch in/out feature amounts to approximately 1.5-2% cost savings on hourly work. By being able to spot drivers punching in too early, you can save about ~5-10% and by picking up on people punching out too late you save ~10-20% of your shift cost.
With data from your tracking system you can save on driver spend.
There’s more on the subject of savings. Because of GPS tracking, a vehicle’s exact route is documented. You can verify that drivers are taking the most cost-effective routes because you have the data collected from your asset tracking solution. Hourly work aside, there’s real value in being able to identify when unapproved routes are taken ~5% of the time.
Data helps you cut unnecessary costs from drivers taking deviant routes.
Increase Efficiency by Tracking Your Assets
In addition to saving on costs, there’s another benefit tucked (like the fold-away screwdriver) into an asset tracking system--increased efficiency. Scheduling, dispatching and back office functions are all impacted when companies implement cloud-based asset tracking software solutions.
Rather than trying to piecemeal together a schedule on a whiteboard or using some other manual process, you can effortlessly create a schedule--days or even weeks in advance. Digital scheduling allows you to manage change orders, create bulk orders and reassign haulers in significantly less time--with less frustration, too. TRUX solutions use drag and drop technology to make scheduling and dispatching even more efficient and fluid.
Many of the tedious and time-consuming back office tasks are simplified and streamlined with asset tracking. Digital tickets eliminate the need for haulers to keep up with their load slips. That means the back office no longer will need to sort and batch tickets at the end of the day or waste time trying to track down the information they need to confirm a job or create an accurate invoice. Because the data is collected and stored in the system, it’s all done automatically for them.
Here’s where the data reveals an area of savings that’s pretty exciting. Replacing manual tasks with automated processes can save the back office 30 minutes per driver per week. Those half hours quickly add up to a potential 728 hours per year. And because time means money, there’s a positive impact on the bottom line.
Data from digital tickets and automated invoices ease the burden on the back office.
Gain Insights with Asset Tracking Technology
Beyond the cost savings and increased efficiencies you’ll realize from putting your data to use, asset tracking, like the can opener tool, reveals opportunities for developing and implementing strategies for higher levels of profitability and safety.
For instance, after studying the data that’s been collected over a period of time you see a concerning number of accidents along a route that’s routinely used by your drivers. Without data, you can’t ascertain whether the cause is the route itself, surrounding conditions or driver behavior. With data, however, you can dive in and discover the source of the problem and make adjustments to reduce the risk of accidents in the future. That adds up to important savings all around.
That’s just one example of how data from an asset tracking solution can work for you. While the technology is continuously collecting and analyzing all sorts of data, you’re equipped to achieve easier and faster compliance, auditing, forecasting and estimating.
Data-driven decisions are easier to make with asset tracking solutions.
TRUX Your All-in-One Tool for Asset Tracking and More
Major players in the construction industry--dump truck fleet owners, contractors and material producers--are looking for ways to significantly streamline their operations. They desperately want to take the frustration and hassles out of daily manual tasks. And they’re actively planning to scale for growth. To meet all these goals and more, they’re finally beginning to see the potential in asset tracking.
It’s understandable that most people still think asset tracking does just--and only--what the name implies. For sure it’s accurate and dependable for keeping tabs on vehicles and equipment, but there’s so much hidden inside this versatile tool:
- Real-time visibility to improve asset utilization and customer service
- Cost savings on labor, fuel and materials
- Increased efficiencies when it comes to scheduling and dispatching
- Time and cost savings in the back office
- Reliable, personalized data to inform critical decisions
Every day, TRUX customers are leveraging the benefits of our asset tracking solution to improve their workflows, trucking logistics, safety procedures and compliance issues.
After comparing all the top tracking solutions on the market, they chose to be TRUX customers for one important reason: TRUX was built especially for the specific needs of businesses that rely on dump trucks to keep the wheels turning.
TRUX has built a solid reputation as the largest network of technology-enabled dump trucks, but one that’s easily accessible. It’s known as powerful, but flexible. With a team that’s tech-driven, but always ready with a helping hand.
Related Posts
Best Way to Logistics Tracking in a New Age of Project Management
Importance of Tracking Asset Utilization for Fleet of Dump Trucks
When you look at your fleet of dump trucks, do you see them as half full or half empty? It’s not a...
Asset Tracking Software Tool & System for Construction Operations
Asset management is leaning more and more heavily on digital tactics to streamline operations and...