7 min read
Why Material Producers Are Leveraging Dispatch Solutions
By: Merril Guzman on Apr 4, 2022 9:00:00 AM
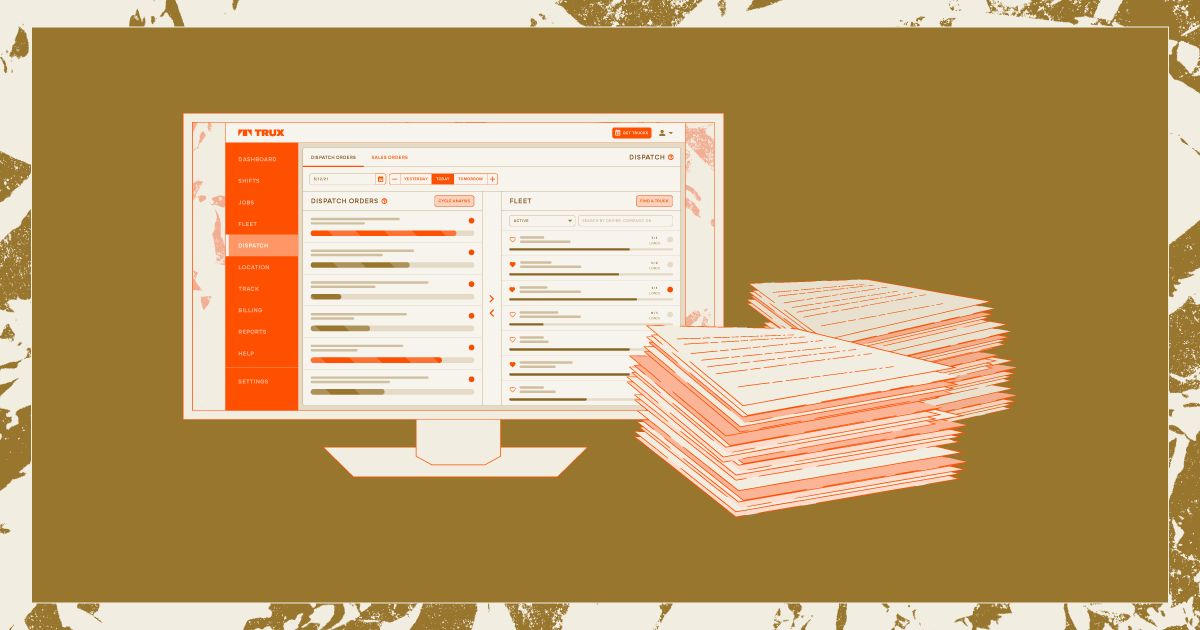
Are you wondering why so many material producers are leveraging dispatch solutions? Perhaps the better question may be why aren’t more material producers leveraging such powerful technology? These digital tools have the potential to overhaul their operations in just a short amount of time while giving them a significant ROI and competitive edge.
By eliminating many of the clunky, time-consuming manual processes that slow down your everyday operations, logistics solutions streamline your dispatching, increasing driver productivity. They provide visibility and data for better decision making, clearer communication, and better customer service. Additional benefits include a way to combat labor shortages, increase your bottom line and elevate the role of dispatcher as well as upskill your current employees.
A Hands Off Approach Can Make All the Difference
In your operations there are a handful of workflows that are driven by manual processes. Paper-based manual processes are inefficient for a number of reasons. They take longer to complete and don’t always account for real time information. They’re prone to human error, including inaccuracies in the information reported and the possibility of being lost. Finally, the documents must be organized and stored somewhere.
Let’s look at a few of the common manual processes that can bog the flow of work and how using a digital dispatch solution improves them:
Creating a schedule and assigning haulers
Normally, a dispatcher spends a good chunk of time in front of a whiteboard or with spreadsheets to come up with a workable schedule. A dispatch solution that features drag and drop dispatching makes the task of schedule creation much easier and faster.
Managing the schedule, company personnel and users, in a single platform means reassigning and reordering are nothing to stress about. Finally, they can also use loadstacking and staggered arrivals to increase hauling efficiency–even to the point of being able to increase the number of loads delivered in a day.
Tickets changing hands
When you depend on haulers to keep up with paper load slips there’s always the risk that once in a while a ticket will go missing. Or you’ll have some that you can’t read. So you end up having to waste time hunting down the load slip or verifying numbers scrawled on the paper. With a dispatch solution, all the information regarding a load is collected and recorded digitally then it’s immediately uploaded into your system.
Digital load slips mean you have accurate and complete documentation for each load delivered. And that saves you from absorbing the cost from a load you have no ticket for. Your back office is saved from spending time sorting and batching. And digital tickets allow you to close out jobs faster. Plus, everything is stored in the cloud for easy, quick access when you need it.
Keeping customers informed
You might not think of this task as a manual process, but think about it. Usually what happens is your dispatcher has to field calls from customers who are curious as to the status of their delivery. Keeping your customers in the loop is crucial to providing excellent customer service, but it’s also very hands-on, and how dispatchers are able to communicate with customers can make or break your ability to increase efficiency.
If you use a dispatch solution that includes an order tracking feature, you’re able to offer a level of customer service that many in construction businesses aren’t used to during their workday. (Keep in mind, they are, however, beginning to have high expectations because of Amazon and pizza delivery!) Not only does order tracking provide immediate answers to a customer, it frees up your dispatcher to focus on other aspects of the job.
Base Decisions on Reliable Real-time and Historical Data
A dispatch solution is positively eye-opening. GPS tracking in real-time gives your dispatcher a big picture view of all active trucks and their locations.
Dispatchers will be able to see where trucks are relative to each other, the jobsite and the plant or quarry – this is essential for communicating. When a situation that may or may not be our of your control, like severe weather, a jobsite entrance being closed temporarily, the need for emergency services, or some other unpredictable event arises, they have the total scene in front of them and can quickly adapt to prevent or lessen delays.
Dispatchers don’t have to call individual haulers (or other company personnel) or send group texts and wait on the answers before they can make a decision. Once the dispatcher decides on the best course of action, they can manage the changes themselves and simply send the updated information to everyone who needs to know through the solution’s built-in communication system. No one is second-guessing or left out of the loop.
Another way GPS tracking enhances and benefits your decision-making is that the real-time data becomes historical data, meaning you will now have accurate data on your cycle times to analyze. Dispatch solutions take the data collected from specific points during the life cycle of a load to give you insights into where inefficiencies are slowing you down.
Without this technology, you can only guess at where you should make changes. Are haulers spending too much time loading? Or unloading at the jobsite? It could be that their routes aren’t optimized or they’re spending way too much time idling in line somewhere along the way. A logistics solution identifies the problem so your efforts to decrease delays are targeted at the right place.
Flexibility is the Key to Dealing with Labor Shortages
Dispatchers must be able to multitask, but even the best of them will struggle (and stress out) when faced with a reduced labor pool. With the help of more efficient workflows, dispatch software enables dispatchers to do more with less–especially if the solution offers a mobile app.
Giving your dispatcher the flexibility to do their job from anywhere not only saves time and increases productivity, the new-found freedom enhances their work-life balance and boosts their job satisfaction. In fact, companies see a 12% reduction in turnover when employees are able to work remotely part of the time.
Another way digital solutions can combat labor shortages is by expanding your potential workforce and personnel to include persons who traditionally haven’t worked in construction. In addition to showing that the construction industry is indeed ready for a digital transformation (with 71% of respondents saying going digital is a priority), a recent survey indicates that dispatch solutions enhance productivity, streamline construction jobs and open up more opportunities for women to enter the industry.
Use Dispatch Software to Increase Your Bottom Line
There are plenty of strategies to increase your construction businesses’ bottom line and eliminate problem areas. One that falls into the easier-said-than-done category is to become more efficient, or more specifically, deliver more material in the same amount of time. A few of the obstacles to streamlined operations are:
-
A lack of visibility
-
Unexpected delays
-
Paper-based manual processes
Here’s a breakdown of how the delivery process looks like for material producers who aren’t tapping into the power of a dispatch solution.
- All dump trucks and vehicles arrive at the plant locations or quarry to load up at about the same time. The result is a line, so there’s waste in time and fuel usage.
- At the scalehouse, again there are lines while haulers wait on those handwritten tickets. In addition to taking up time, handwritten paper load slips can get lost. A lost ticket is a loss.
- In the dispatch office, phone calls and texts can overload your dispatcher. Without visibility into all your active trucks’ whereabouts, your dispatcher can’t optimize schedules in real-time.
- If you use third-party haulers, you have yet another blindspot. Things can easily get off track without visibility into their activity.
- At the jobsite the foreman is in the dark and doesn’t know when to have the crew ready for a truck’s arrival unless they contact the dispatcher–who is most likely dealing with other inquiries at the moment. The truck arrives only to wait for the site to be prepared.
Now, here’s a look at how digital technology transforms operations, streamlining processes to save time, effort and fuel.
- You can monitor the number of trucks and how quickly they're moving in and out of the plant or quarry. Accurate data gives you insights into load times and allows you to compare multiple plants or quarries in a particular region.
- Digital load slips are safer, faster and more accurate. Haulers stay in their trucks which protects them and saves time. The load data is recorded and instantly sent to the back office where invoices are automatically generated and consolidated. No more missing load slips means you can count on being paid for every load delivered.
- Instead of fielding calls, your dispatcher uses the built-in communication system to keep everyone, including field personnel updated. When change orders come in (or new orders), they have a bird’s eye view of all active haulers and can quickly adapt to reduce the potential for delay.
- Systems like Trux allows you to manage your hired haulers the same way you do with your internal haulers.
- Jobsites run more efficiently because they have access to the information they need. Instead of preparing for an arrival early and then waiting, their work can be planned down to the minute, increasing productivity and reducing inefficiency.
By providing a big picture view of operations and hauling, enabling dispatchers to optimize routes and eliminating time-consuming paper processes, dispatch solutions are an effective way to protect your profitability and streamline your services.
Trux: The Dispatch Solution for Material Producers
Trux is the all-in-one dispatch solution for material producers that ticks all the boxes:
-
Replaces manual processes with streamlined digital processes
-
Provides greater visibility and better communication
-
Makes it possible to do more with less to combat labor shortages
-
Helps protect your profit margins
-
Enhances your employees’ contributions to your overall success
-
Gives you a competitive advantage in the market with increased customer service
Want to find out specifically how your organization benefits from adding a dispatch solution like Trux, and how it can help your business’ specific needs? This 5-minute logistics assessment is a good place to start.
Related Posts
How Dispatching Software Enhances Logistics and Material Hauling
In today’s competitive construction industry, efficiency in logistics can make or break your...
10 Best Dispatch Trucking Software Features: Cloud-Based and More
Dispatch Trucking Software Elevates Role of Dump Truck Dispatcher
With dispatch trucking software at their disposal, dispatchers at materials companies and large...