8 min read
Plant Optimization: Every Material Producers’ Goal
By: Matthew Hennessy on May 17, 2021 10:45:00 AM
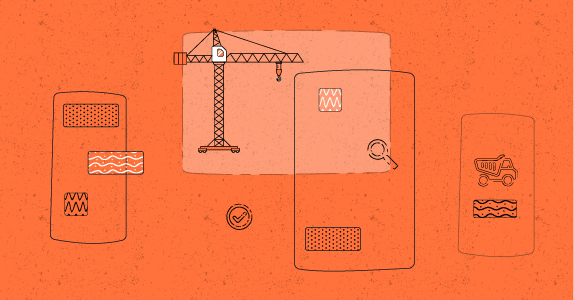
Do you operate one plant or hundreds? Do you rely on pickups or do you take control of material delivery? Regardless, you probably care deeply about having a streamlined operation and you seek the information to monitor and optimize your plant performance. You also likely have realized there is not an obvious or singular way to achieve this today. The goal of this article is to help guide your approach to realizing efficiencies and attaining plant optimization.
Understanding and Componentizing Efficiency
“Efficiency” and “optimization” are words used too often in a highly generalized fashion. Yet, despite their frequent buzzword status, notions of “efficiency” and “optimization” wield incredible power to your business, especially when understood in their hyper-specific and actionable sub-components.
Short-haul aggregates and asphalt logistics provide the perfect example of this. Oftentimes the industry looks to optimize “cycle time.” Yet, “cycle time” breaks down into several key elements, each with its own set of efficiency drivers and actions.
For example, improving the drive time to and from a delivery location requires drastically different insight and action than improving the time taken to load the truck or unload the truck. Furthermore, as a material producer, you have different degrees of control at the various stages of the cycle. There’s nowhere you have more control over efficiency than at your own plant. It is with this realization that material producers are looking to take the reins in their own backyard and focus on plant optimization.
Why Care About Plant Optimization?
Many of the material producers leaning into plant optimization understand three key value levers that efficiency will provide them:
- Improved unit economics
- Incremental capacity and revenue
- Enhanced customer and partner retention
These material producers are painfully aware that every extra minute a truck takes to get loaded represents...
- A minute someone is paying for - perhaps the material producer themselves
- A minute in which more material could have been delivered
- A minute the customer could be getting frustrated for having picked their company for the job
Each moment of confusion or misalignment is a risk...
- A risk you could over-produce HMA and let thousands of dollars of material go to waste
- A risk you might have to say “no” to a customer’s order because you do not have the material on hand
- A risk you might under-deliver on a project because you could not keep pace
- A risk a driver will decide they would rather work for your competitor because they are just not earning enough money waiting around to get loaded
- A safety risk...after all, every time someone drives onto your plant you take on liability. Get the truckers turned around as fast and smoothly as possible!
Material producers fully engaged in plant optimization have made the calculation that they do not want these costs and risks on their shoulders.
Plant Optimization Solutions That Are Attainable Today
Despite the clear value in maintaining plant optimization, material producers currently have surprisingly little visibility into how efficient or inefficient they really are. There is not a ubiquitous market solution. For example, very few material producers can see, in real-time (or retrospectively), how their plant load time is trending or how their material quantities on hand match up against forecasted demand. In fact, material producers that have a grasp on metrics like plant load time are often collecting data with an army of interns using stopwatches and clipboards.
While perhaps this manual approach is better than nothing, it will not provide an understanding of plant efficiency in a scaleable, holistic, or actionable way. Furthermore, it is not going to provide efficiency in any componentized view; there will be no visibility into why or how the truck took 47 minutes to come back through the plant gate 22 tons heavier. Did it get stuck at the scale house? Did it get stuck at the loading point? Was there a staggering mix-up? You simply would not know.
Solving the Plant Optimization Problem with Technology Platforms
This is where technology platforms are starting to provide practical solutions to help material producers realize efficiencies and value across their plants and quarries. Phone-based GPS tracking through plant geofences provides the quickest and easiest path to data collection that can inform plant efficiency. This then needs to be paired with a highly interconnected platform with multiple data types layered on to your GPS data. After all, GPS data is most valuable when paired with information on order volumes and stockpile quantities, with information about how many drivers are headed to your plant right now, with weather forecasts, and with many more metrics. The reason you need this level of platform scope is that plant inefficiency is driven by a multitude of multifaceted and interconnected factors.
So, What are These Causes of Plant Inefficiency?
Through our work helping customers with plant optimization, we have come across a whole host of common causes of inefficiency. While weather is the least controllable factor we see leading to inefficiency, it is, thankfully, predictable...especially with the help of platforms with trucking-specific forecasting embedded. Fortunately, many of the other factors leading to inefficiency are well within the material producer’s control:
- Problematic plant layouts
- Unreliable and slow loading machinery
- Material types that are difficult to load with existing practices
- Bad truck staggering leading to bottlenecks at loading points and ticketing houses
- Poorly planned plant operating hours or early-morning preparedness
- Running out of material
- Cash payments consuming disproportionate time
Any truly effective platform needs to have direct and easy visibility into all these factors and more.
Your platform needs to be able to provide visibility both in real-time as well as retrospectively. Amidst the hustle and bustle of plant operations, your employees need every tool possible to help them make decisions in real-time. They need visibility into which trucks are inbound to the plant, which trucks have been waiting the longest to get loaded, which jobs are running behind and need prioritizing, which material is about to run out unless the stockpile or silo is replenished, etc..
In short, you need to empower employees at the plant to take the reigns of the operations to deliver that optimum customer experience.
The Need for An Analytics Partner in Your Efficiency-seeking Journey
In addition, you need advanced analytics to provide benchmarking, generate accountability, identify problems, and recommend solutions. You need the highest quality information with the utmost usability and accessibility so that you waste less time collecting or manipulating data and can spend more time solving the problem.
Perhaps the most important aspect of any platform’s analytics offering should be the company’s commitment to partnering with your organization in achieving your goals. This may seem surprising given how technology is so often sold with a “set-it-and-forget-it” approach. However, plant optimization requires more than a dashboard tossed over the fence to you by a sales rep.
The reason this partnership mentality is so important is that to truly achieve plant optimization requires a fundamental culture shift within your organization. On the ground, you need scale clerks, loaders, and plant managers all seeking to improve their metrics. You need your employees to take pride in hitting their metrics and perhaps engaging in healthy KPI-driven competition. This culture needs to boil up to regional and division leaders all practicing knowledge-sharing surrounding plant efficiency.
A robust analytics product provides the foundation for this culture, but to effectively train and empower users with such a powerful product, and to enable the strategic and nuanced conversations and approaches to plant optimization, requires a consultative and humble partner continually listening and engaging with all of your stakeholders.
As a side note, any good partner should want to do this - after all, listening to customers is how technology companies can best meet your needs and achieve success with you.
Perhaps most importantly, you need to find a partner willing to customize and iterate the product to meet your specific needs. After all, there are always going to be unique complexities to a material producers’ plant operations that must be accounted for. Anything truly “off the shelf” is likely not the ultimate tool your organization should seek in enacting the culture shift surrounding plant optimization.
It is this exact collaborative and consultative approach Trux takes to working with our customers. We believe our customers’ results from this approach speak for themselves. For example, in Q3 of 2020 we started a consultative relationship and launched a customized “Load Time Suite” for a customer with 40 quarries and roughly 1000 loads per day. Almost immediately, together, we were able to move the needle. Three quarters later we have helped the customer shave 15% off their average plant load time, saving nearly 50 hours per day.
In Conclusion
For a material producer concerned with maximizing their plant efficiencies and seeking a technology partner, our final recommendation is simple: don’t rush. Plant optimization is a complex and multifaceted problem interwoven with your company’s unique operational dynamics. Take your time to find the most interconnected modern construction technology platform with a track record of helping customers optimize their plants. Patiently seek the organization most committed to being a true partner in your continual efficiency-seeking journey. Without this approach, you could all-too-easily end up with a subpar solution causing more confusion and pain with no immediate help on the way.
If you are interested in transforming your plant operations with a dedicated partner, the best way to get started is to connect with one of our logistics experts. Scheduling a demo brings you one step closer to realizing your goal of increased plant optimization.
Related Posts
How Material Producers Get Ahead with Dump Truck Technology
Of all the deliveries you’ll make this next year and moving forward, perhaps the most important is...
What is a Production Meeting? How Contractors Can Improve Them
What is a production meeting? Daily production meetings are a critical tool for construction teams...
Why Material Management is Important for Plant Production | Trux
Running an asphalt or concrete ready-mix plant underscores the importance of running your material...