9 min read
Utilizing Software to Navigate Complex Scheduling: A Trucking Dispatcher's Guide
By: TRUX Team on Sep 19, 2023 7:30:54 AM
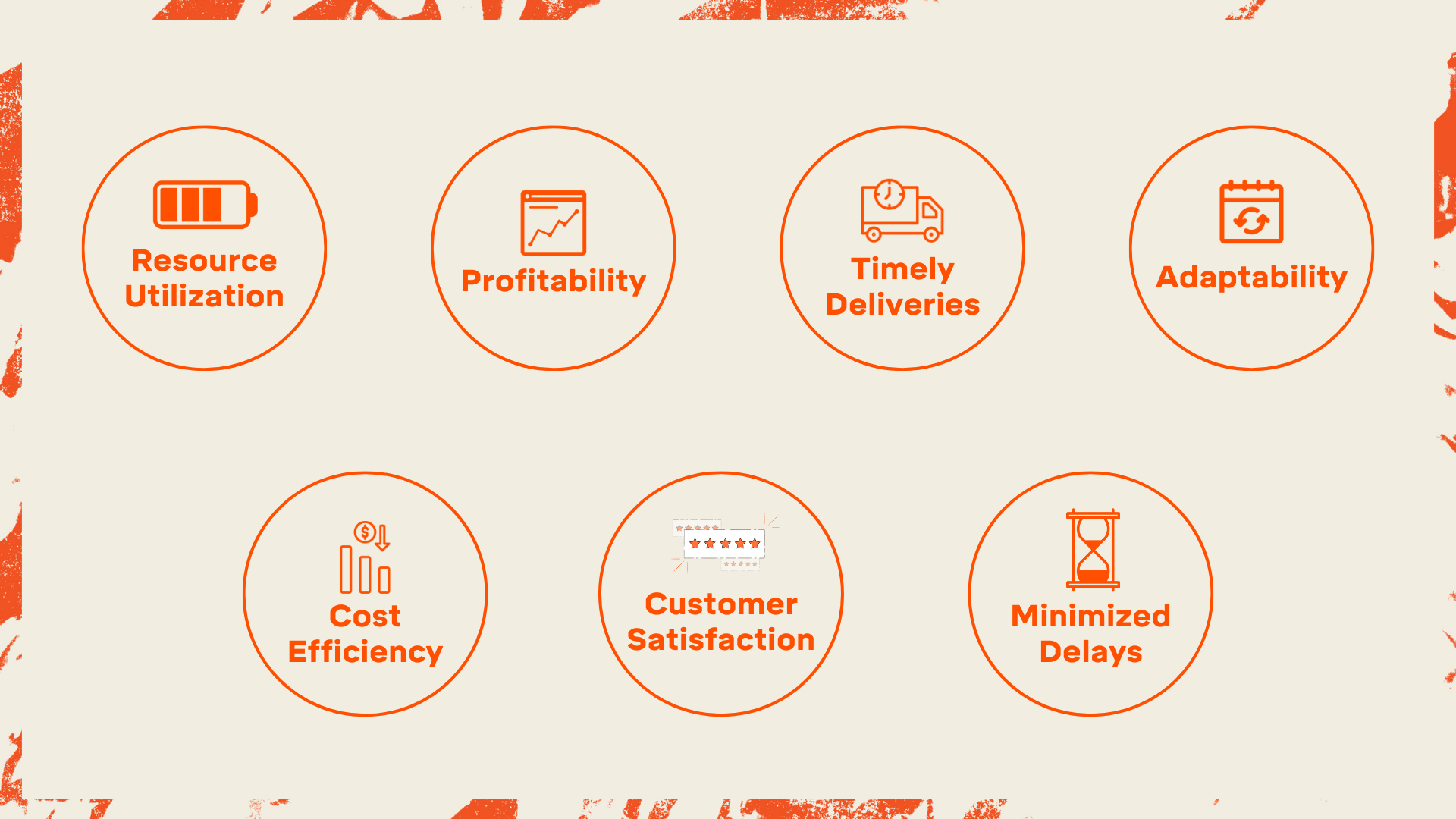
Complex scheduling is a major challenge for trucking dispatchers. This article provides practical tips to navigate this challenge and ensure efficient operations. Download the accompanying eBook: A Dump Truck Dispatcher's Guide to Efficient Scheduling at the end.
Click a topic below to jump to the relevant section:
The Pivotal Role of a Dispatcher in Hauling Operations
Key Challenges in Traditional Dump Truck Scheduling
Key Features to Look For In Dispatch Software
Harnessing Real-Time Data For Proactive Scheduling
THE PIVOTAL ROLE OF A DISPATCHER IN HAULING OPERATIONS
Dump truck dispatchers play a crucial role in the efficient and smooth operations of a dump truck fleet. Their responsibilities are multifaceted and require a combination of organizational and communication skills, logistical expertise, and local market knowledge. Effective load planning and scheduling, in particular, holds immense significance in ensuring the optimal use of dump trucking resources, timely deliveries, customer satisfaction, and overall profitability.
Effective scheduling has the potential to impact the following:
- Resource Utilization: Effective scheduling ensures that your dump truck resources are utilized optimally, reducing downtime and maximizing revenue generation.
- Timely Deliveries: Proper scheduling helps ensure that deliveries are made on time, meeting customer expectations and building a reputation for reliability.
- Cost Efficiency: Optimized routes and schedules lead to reduced fuel consumption, lower maintenance costs, and decreased operational expenses.
- Minimized Delays: Along with real-time tracking and monitoring, effective scheduling minimizes delays caused by traffic, weather, or unforeseen events.
- Customer Satisfaction: Meeting delivery deadlines enhances customer satisfaction, leading to repeat business and positive word-of-mouth referrals.
- Adaptability: An effective schedule can be quickly adapted to changes and challenges, maintaining operational continuity even in the face of disruptions.
- Profitability: Ultimately, effective scheduling directly impacts the bottom line. By minimizing inefficiencies and maximizing throughput, profitability is enhanced.
KEY CHALLENGES IN TRADITIONAL DUMP TRUCK SCHEDULING
Managing and scheduling dump trucks is a complex and challenging task, especially without the benefit of dispatching and planning tools. Dispatchers must overcome some of the common scheduling hurdles.
Receiving and Managing Customer Orders
The process starts with a customer order for materials. But turning that “sales order” into a dispatch order and that dispatch order into individual loads to be assigned to multiple haulers takes a lot of time. The more time your dispatch office spends on managing this order intake and assignment process, the less capacity you have to fulfill these orders.
Utilizing Existing Hauling Capacity
Ensuring that each dump truck is utilized optimally to match demand while avoiding overloading any individual truck can be tricky.
Finding Additional, Reliable Hauling Supply
When demand spikes or there are unforeseen disruptions, securing additional dump trucks on short notice can be difficult. Finding reliable subcontractors or haulers who can meet the required quality and capacity standards is essential.
Load Planning
Striking the right balance between assigning enough trucks to fulfill an order while avoiding over-trucking (which leads to inefficiencies and increased costs) or under-trucking (which causes delays and customer dissatisfaction) is a complicated process. It requires a combination of detailed local knowledge, an understanding of truck types and requirements, and forecasting how many loads and trucks will be required to complete an order.
Communicating with Haulers
Coordinating with multiple haulers and ensuring they receive accurate instructions for pickups, deliveries, and any special requirements can be challenging. And the reverse is also true - dispatchers need to know when a hauler has seen their request and confirmed that they will be able to take the job. Manual communication increases the likelihood of miscommunication and errors.
Communicating with Customers
Providing accurate and timely updates to customers about the status of their orders, estimated delivery times, and any changes helps build trust and manage expectations. Manually communicating these updates is very time consuming for both parties and can even lead to inconsistent information.
Monitoring Delivery Progress
Keeping track of the progress of each truck, monitoring whether they are on schedule, identifying potential delays, and adjusting the schedule accordingly can be time-consuming and error-prone without proper tracking systems.
Managing Changes
Sudden changes in orders, delays due to weather or traffic, breakdowns, and other unforeseen events can disrupt the entire scheduling process. Handling these changes while minimizing disruptions requires quick decision-making and communication.
Data Management
Keeping track of all relevant data, including customer orders, driver schedules, routes, delivery statuses, and scale/ticket data can be overwhelming without a robust data management system.
KEY FEATURES TO LOOK FOR IN TRUCKING DISPATCH SOFTWARE
Scheduling software tools have the power to enhance the precision and efficiency of your dispatch operations. No matter which system(s) you use, make sure it offers the following features and functionality.
Integration
Sales order and scale system integration is key to efficient order and ticket data management. Typical integration messages exchanged between Trux and customer systems.
Tools to Utilize Existing Capacity
A comprehensive dispatching platform tells you which of your haulers are fully-scheduled and which have unscheduled capacity for more assignments. And because the system is tracking each hauler, you will be aware of which trucks are nearby the plant and available to take additional loads throughout the day.
Access to More Trucks
While it may not seem like access to a supply of 3rd party haulers has anything to do with software, effectively finding and managing independent haulers without it is very time consuming and inefficient.
For starters, all available haulers on the Trux Marketplace are verified and current with respect to insurance and similar regulatory requirements. And when you have a need to find more trucks, Trux software allows you to just post your job requirements and then notifies all approved haulers in the local area who can review and claim the work. Once claimed you receive a notification that the work has been scheduled. No more back-and-forth texting and calling to check on availability.
Once the work begins, Trux allows you to stay on top of progress from the moment the hauler(s) punch in to the moment they punch out including access to digital load slips, hauler location, and ETA.
Finally, when the work is complete, you will only receive a single, consolidated invoice for all of the hauling your sourced from the Marketplace - no matter how many haulers or hauling companies you used. And Trux, in turn, will pay the haulers. This saves you up to 1.5 hours of business office time per hauler per week.
Load Planning Tools
Being over- or under-trucked is a constant challenge for dispatchers when trying to put together the day’s schedule. Load planning tools help you automatically calculate the number of loads, trucks, and/or tons needed to complete each order while taking truck type, travel time, and turn times into consideration. If the order is based on TONS, Trux will calculate how many loads and trucks are required. If the order is for a certain number of loads, Trux will calculate the number of tons to be delivered.
Hauler Communication Tools
An effective scheduling system should enable dispatchers to automatically notify haulers when they’ve been requested for or assigned work, when it’s time to punch in, and when their schedule has changed. It should also provide them with a simple way to communicate detailed job instructions with each job and see when assignments have been accepted by a hauler. That kind of 2-way communication is critical to avoiding confusion, delays, and wasted resources.
Customer Communication Tools
Your customers now expect (and deserve) more information and transparency about their deliveries. A comprehensive dump truck logistics solution must include the ability to give your customers the power to track their entire delivery and the tools to improve job site productivity. As soon as a dispatch order is created, you should be able to send an Order Confirmation to your customer with information on the product, quantity, number of trucks, delivery window, and delivery location to reduce the chance of miscommunication or errors. The system must also allow your customers to track their entire delivery and every truck from the plant to the job site, and everywhere in between. This kind of visibility and transparency will strengthen your customer relationships and lead to repeat business and loyalty.
Monitoring Delivery Progress
Hauler tracking has long been a basic expectation for a dump truck logistics system. Your dispatchers need to know in real-time where every active hauler is, their direction of travel, and their approximate ETA. And knowing the full route history on completed loads lets you know whether they are taking the most efficient routes. But as important is having the ability to monitor, in real-time, the overall progress of every customer order. Your team needs to know
which orders are on, ahead, or behind schedule and which need focus and attention to keep them on track.
Load Stacking and Reassignment
Change is inevitable on a daily basis. Changes to orders, truck and equipment breakdowns, traffic, weather, etc. How quickly can you adapt the schedule to these changes when they happen?
Trux makes it easy to stack and order all of a hauler’s assigned loads an entire day. When you need to make changes to accommodate the unforeseen, dispatchers can easily drag and drop a scheduled load to rearrange the order of upcoming loads throughout the day. Each time a hauler completes a load, they will be prompted to begin the next load and alerted to any changes in the order or location of their next assignment. So making and communicating changes occur instantly and with automatic notification.
E-Ticketing
Eliminating paper from your operations is not only the smart thing to do from an efficiency standpoint, it’s also becoming the norm on construction sites almost everywhere. No more distributing, managing, and exchanging paperwork between the scale house, the hauler, and job site personnel, All scale ticket data from completed deliveries are stored and available to export and download from Trux, including ticket numbers, E-Tickets, truck ID, hauler information, punch-in, unload, and punch-out times, total loads and tons, and more.
Advanced Planning
Last-minute and even same-day orders can be the toughest to schedule and fulfill. But they certainly don’t represent all of your orders and deliveries. For the rest of your orders, you have the ability to plan ahead by assigning loads to haulers one or more days in advance. Set them up as “draft” and release them with a single click once you know that weather, schedule, and other factors are on-target.
HARNESSING REAL-TIME DATA FOR PROACTIVE SCHEDULING
Real-time data is essential to enabling dispatchers (and customers) to track trucks, loads, and deliveries throughout the day. But this data also provides insights to help dispatchers make scheduling decisions throughout the day. With real-time tracking and location data, dispatchers will know which of their trucks are at the plant/start location and unassigned. These are haulers who are willing and able to take unassigned loads. Similarly, real-time data enables dispatchers to know which drivers have completed their assigned loads but are available and willing to take more. These are drivers who remain “punched in” indicating they are ready and willing to take additional loads.
Real-time data also enables trucking dispatchers to monitor the velocity of deliveries throughout the day. Most people understand how being too slow will negatively impact project progress. But faster is not always better, especially with materials like asphalt that have a shelf life or expiry. Too much of this material just sitting around won’t be able to get used and will go to waste. And deliveries of other materials that come too fast could back things up at the job site. Finding the optimal speed can be critical for project success, and that requires real-time insights.
Learn more about how dispatching software can help with the critical and complex task of dump truck scheduling in this eBook.
Frequently asked questions
Q: How does software assist in preventing scheduling overlaps and conflicts?
A: Modern dispatch software provides real-time visibility into hauler utilization and availability. It can automatically flag potential conflicts, helping dispatchers make adjustments and ensure smooth operations.
Q: How can dispatchers use software to handle unexpected delays or changes?
A: Dispatch software features quick rescheduling and real-time communication tools. When unexpected changes arise, dispatchers can easily reassign, re-order, and re-stack drivers’ schedules and automatically alert them to these changes on the fly.
Related Posts
The Impact of Efficient Dispatching on Customer Satisfaction
In this article, we will explore the vital role that dump truck dispatchers play in ensuring smooth...
Mastering Dispatch Management in the Dump Truck Industry
Dispatch management plays a pivotal role in the efficiency and profitability of operations within...
Dispatch Trucking Software Elevates Role of Dump Truck Dispatcher
With dispatch trucking software at their disposal, dispatchers at materials companies and large...